top of page
Quality Troubleshooting
A hypothetical case is used as example in how changes (whether intentional or not) made in suspension polymerization process may result in Quality issues if effects are not foreseen.
INTENDED CHANGE
An initiative to reduce VCM exposure of personnel during reactor's manual cleanings motivated a S-PVC producer to start a Project to look for alternatives to reduce said exposure.
Their additives supplier suggested to replace nigrosin-based antifouling agent (used in original technology) and switch to a high efficiency one based on in-situ polycondensation of phenolic compounds. Additionally, a High Pressure Wash System was designed and installed to clean reactors.
Such combination resulted in a drastic reduction of reactor fouling and almost the complete elimination of manual cleaning operations. As a consequence, jacket´s overall heat transfer coefficient increased and therefore also heat removal capacity of reactor.
PVC producer decided to take advantage of this additional heat-removal capacity and increased the amount of charged peroxides (solution in mineral spirits, as in original technology) through an iterative process to reduce polymerization times and increase Plant Productivity.
The increase in Productivity made the Project economically profitable and therefore a great success … except for a small detail.
UNDESIRED PROBLEM
Customers began complaining due to sporadic appearance of aesthetical imperfections in blown films and extruded thin films. Gels/imperfections were observed as luminous points in transparent films and as local variations in the thickness of articles involving thin films (whether plasticized or not), weakening and in some cases even breaking the film.
No significant Quality deviation was detected using conventional ASTM Quality methods.
To mitigate the problem, they resorted to practical knowledge for the control of Fish Eyes such as intensive reactor cleaning, cross-contamination avoidance with other types of resin, checking of suspension agent solutions, etc.
However, the presence of gels persisted as well as an increasing Customer dissatisfaction and additional costs for Customer Service and additional energy/additives that are needed to melt completely.
UNSUSPECTED CAUSE
In suspension polymerization all VCM droplets ideally should be homogeneous with the same concentration of auxiliary chemicals, so all PVC grains are formed with the same morphological structure. However, in industrial practice this is not the case due to size and time restrictions that result in a concentration distribution of chemicals between droplets.
Zerfa (1994) devised a test with dyed monomer to demonstrate that a period of mixing is required before polymerization begins when using conventional peroxides to achieve homogenization among droplets.
In our hypothetical Plant, a higher amount of peroxides used to reduce polymerization time also reduced the available time to disperse initiators at the beginning of reaction.
As reported by Lukas (1984, 1985) when a polymerization batch with very poor peroxide distribution is observed by optical microscopy, it is possible to find grains with a continuous transition of different external appearance as seen as follows…

SEM images (around x2500) of freeze-fractured grains of this sample show also an internal transition from a loose structure to a compact structure and finally a fused one.


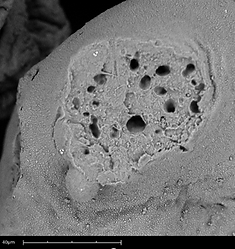
It is evident that PVC grains with loose internal structure will easily absorb liquid additives and crumble during processing, while PVC grains with tightly-packed internal structure incorporate additives slowly (or even do not absorb) and therefore generate inhomogeneous local points.
Commercial S-PVC consists of grains with gradual transition of morphological structures depending on process conditions, and some grains would appear as unprocessable and infusible depending on processing conditions.
By means of optical microphotography it is possible to observe gels in film samples that consist of grains with different degrees of fusion and incorporation into PVC matrix.

BLOWN FILM
Unfused grain

Molten, not incorporated grain

Molten, partially incorporated grain
Partially incorporated grains, due to their different viscoelasticity with respect to the surrounding PVC matrix, would produce small bumps with diffraction phenomena that make them very noticeable in transparent thin films.
GEL DEFORMATION DURING PROCESSING
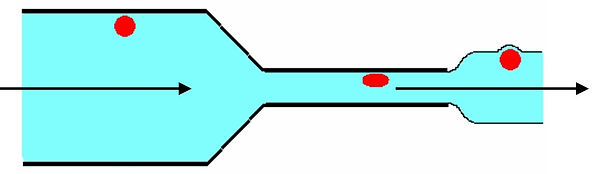
DIFRACTION PHENOMENA CAUSED BY GELS

APPROPRIATE REMEDY
Once the cause of the problem is found, solutions can be proposed.
However, in order to make changes without generating new negative and undesirable effects on Quality it is necessary to take into account the complex time-dependent set of physical and chemical phenomena involved.
Let me help you to understand and optimize your S-PVC external Morphology by either:
- Selecting the better Primary Suspending Agents for your process conditions
- Adjusting your process conditions to keep your Primary Suspending Agents
- Optimizing both your process conditions and Primary Suspending Agents
... to dramatically reduce off-grade product due to Grain size issues, as well as improve both performance and productivity of your PVC resins in your customer's process.
Do you have more questions regarding PVC resins? I have many answers.
View my PROFILE and visit my CONSULTING SERVICES page.
As a Consultant I can offer you a diagnosis of any Quality problem you are having in your PVC resins and offer solutions to eliminate.
Let me help you understand and control your SPVC resins.
View my PROFILE and visit my CONSULTING SERVICES page.
bottom of page